奈良県の東大寺にそびえ立つ「奈良の大仏」。その壮大な姿は、訪れる人々を圧倒し、日本の鋳造技術の高さをうかがい知ることができます。奈良の大仏が作られたのは、約1300年前のことです。現代のように機械のない時代にも関わらず、高さ約15メートル・重さ約250tもの巨大鋳物像はどのようにして作られたのでしょうか?
この記事では、奈良の大仏が完成するまでの過程を解説します✨
なぜ作られたのか?
奈良の大仏が建造されたのは、745年頃(天平17年)と言われています。この当時の日本では、度重なる戦乱や自然災害、病の大流行と人々にとって苦しい時代が続きました。
そんな中、聖武天皇が「仏教の力で国を守ろう」として発願し、大仏造立計画が始まったとされています。
使われた材料は?
大仏を作るために使用された材料は全国各地から集められ、銅が約500t、スズが約8.5t、水銀が約2.5t、金が約440㎏使用されました。
奈良の大仏が完成するまで
それでは、大仏が完成するまでどのような工程があったのでしょうか?
①原型を作る
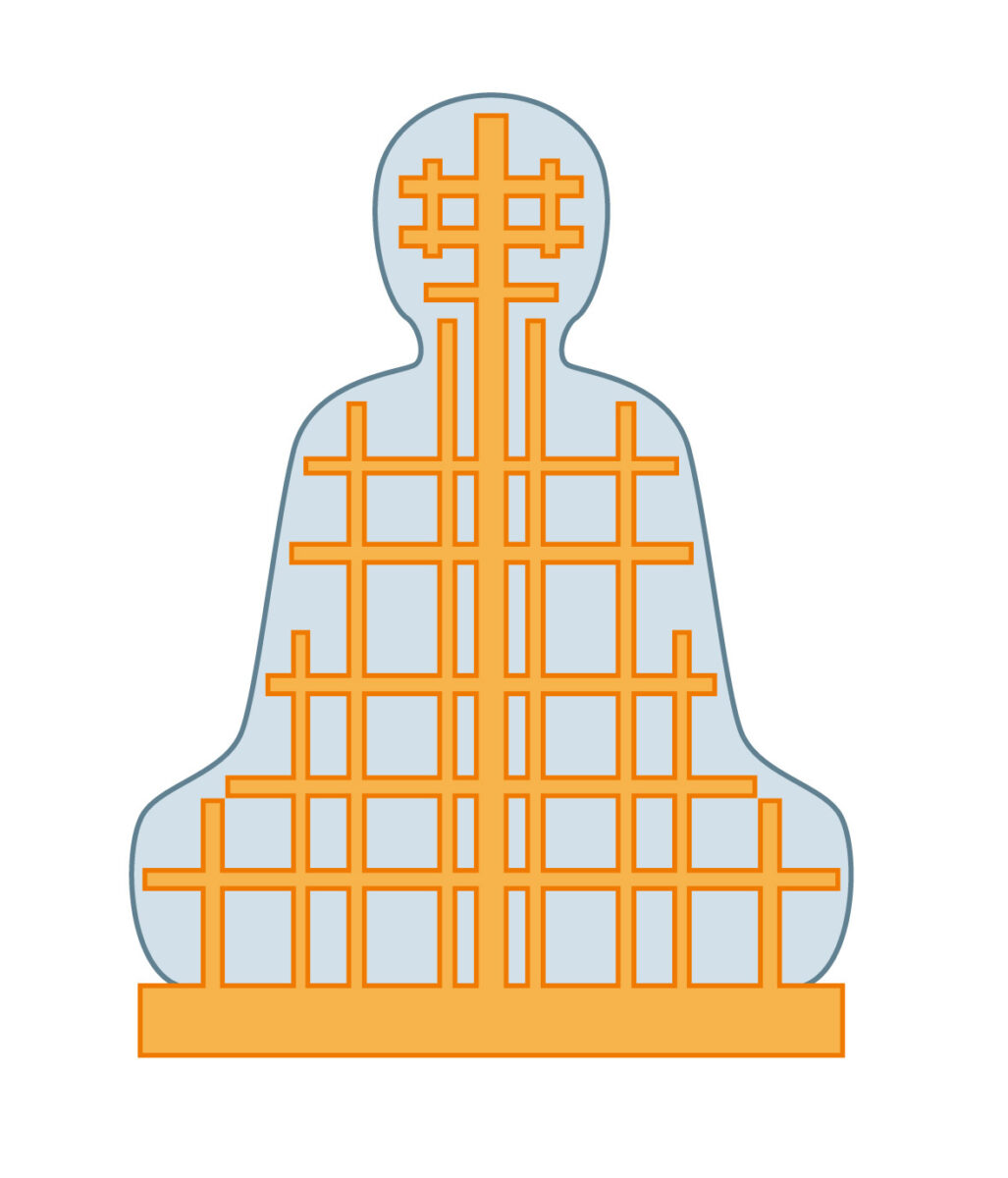
まずは土台に、木や縄で骨組みを作ります。その骨組みへ粘土を塗り原型を作ります。
粘土で全てを塗り終わると、土でできた大仏の原型が完成します。
②鋳型を作る
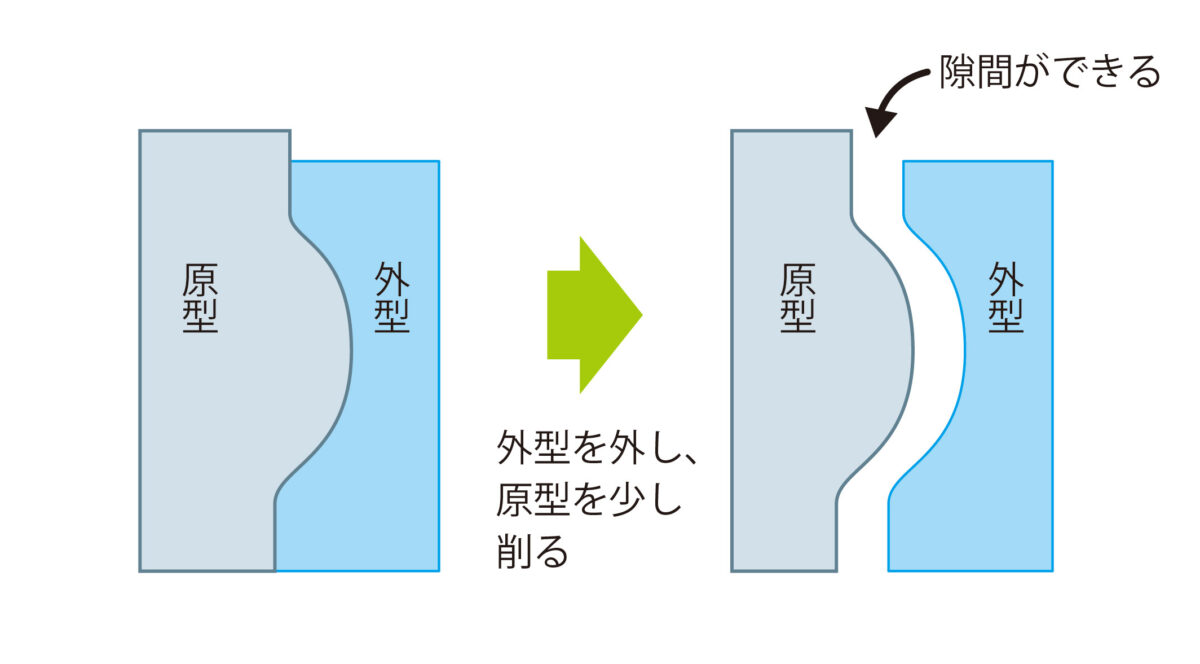
土の大仏の表面を取り囲むように、粘土を塗り外型を作ります。外型を外し、削り中子法と呼ばれる手法で原型の表面を少し削ったあと、外型をもとの位置に戻すと空洞ができ鋳型となります。
奈良の大仏の厚さは約5㎝程度といわれています。
③流し込み
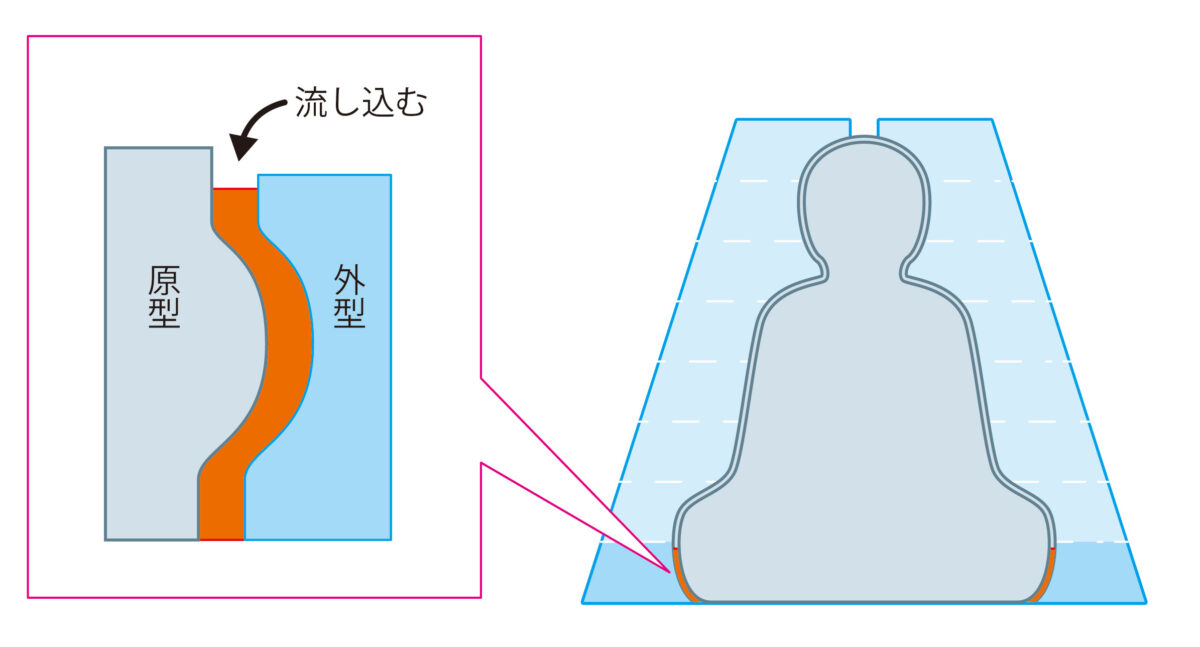
大仏の周りには、材料を溶かすための炉がいくつも置かれ、炉へ銅とスズを入れ、たたらで風を送りながら材料を溶かしました。約1000℃以上で溶かされた青銅(※)は鋳型の隙間へ流し込まれます。この時に鋳型の隙間を一定距離に保つため、型持というつっかえ棒のようなものを挟み込んでいました。
大仏は非常に大きいため、一度にこの工程を行うことは難しいです。
そのため鋳型・流し込みの工程を分け、1段目が終わると周りを土で固め土台にし2段目へ、という風に下から上へと順に8段分を繰り返しながら流し込みが進められていきました。段ごとの境目はつなぎ目が溶けあわずに切れてしまうため、鋳がらくりという手法でパズルのように溶湯が噛み込んで外れないようになっています。
※青銅・・・銅を主成分としてスズを含む合金
④表面仕上げ
頭まで鋳造された大仏は土の中から出され、鋳造欠陥が出た箇所は補修を行い、表面を磨き仕上げをしていきます。当時の奈良の大仏は表面が金で覆われており、これは現代のメッキ加工のような技法で仕上げられました。
金と水銀を混ぜると、アマルガムという液体が出来ます。これを大仏の表面に塗り、加熱する事で水銀が発生し金が表面に残ります。これにより水銀公害なども発生したと言われています。
大仏が座っている台座はこの後に作られたと言われており、完成まで約10年の年月と260万人の労力がかかったとされています。こうした高度な鋳造法と職人たちの手によって、奈良の大仏は完成しました!
古代日本の卓越した技術力は、現在も私たちに感動を与えてくれます。
今回は奈良の大仏の作り方を解説させていただきました!
次回もお楽しみに✨