近年、宇宙開発は急速に進化を続けており、新たなミッションが次々と打ち上げられています。ロケットや人工衛星、さらには月や火星探査機にいたるまで、宇宙開発に関わる先端技術を支えているうちの一つが『鋳造技術』です。
特に、軽量で高耐久な合金の開発や、高精度な部品製造を可能とする最新の鋳造プロセスが宇宙産業に革命をもたらしています。
この記事は、宇宙産業で活躍する最先端の鋳造技術と、その革新がどのように未来の宇宙開発を支えているのかを解説します。
宇宙産業で求められる鋳造技術とは?
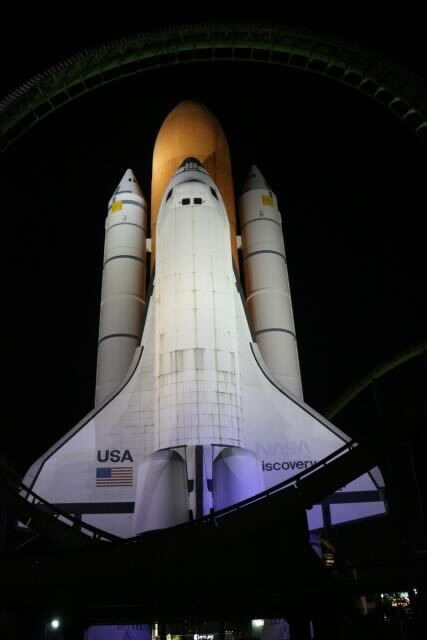
宇宙産業では、極限環境に耐えることができる部品が求められます。
ロケットエンジンの部品は高温・高圧の条件下で動作するため、耐熱性と強度が必要不可欠です。また、人工衛星の構造体や探査機の着陸脚には、軽量化と耐衝撃性が求められます。
宇宙環境向きの材料としては、一般的に金属よりも耐熱性に優れたセラミックや、軽くて高機能な有機ポリマー、カーボンファイバーで強化された複合材料など様々な材料があげられます。その中で金属に求められるのは高強度・耐久性の面が大きくなります。いかに丈夫なまま軽くできるかが重要となります。これらの特徴を併せ持つ金属の代表が、アルミニウム・マグネシウム・チタンの合金です。
宇宙産業に求められる厳しい条件をクリアするため、鋳造技術は日々進化を遂げています。
精密鋳造(インベストメント・キャスティング)
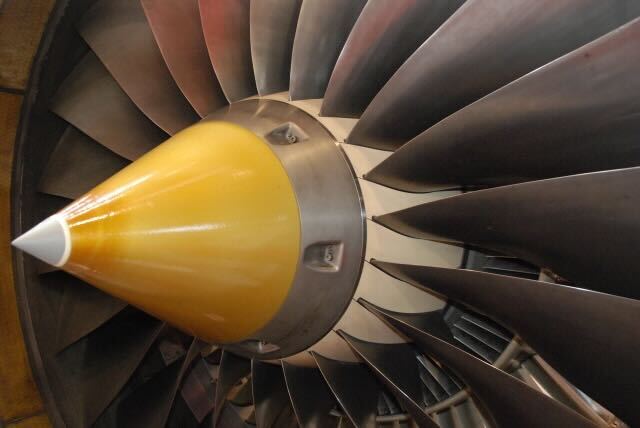
精密鋳造は、ロケットエンジンのタービンブレードや燃焼室など、高い精度が要求される部品の製造に活用されます。セラミックスラリーから鋳型を作るため、細かい形状ができ、鋳肌も綺麗で寸法精度が高い事が特徴です。タービンブレードのようにわずかな芯ズレや凹みでも燃焼効率の低下や事故に繋がる部品は、非常に高いクオリティが求められます。
精密鋳造とは、最高水準の製品製造に不可欠な鋳造技術であり、細かいディテールと複雑な形状を持つ製品に特化しています。航空宇宙産業はもちろん、医療機器、自動車産業でも使用されます。
製造工程は『鋳型・製法による分類~その他特殊鋳造法について~』にて解説しています✨
半固体鋳造
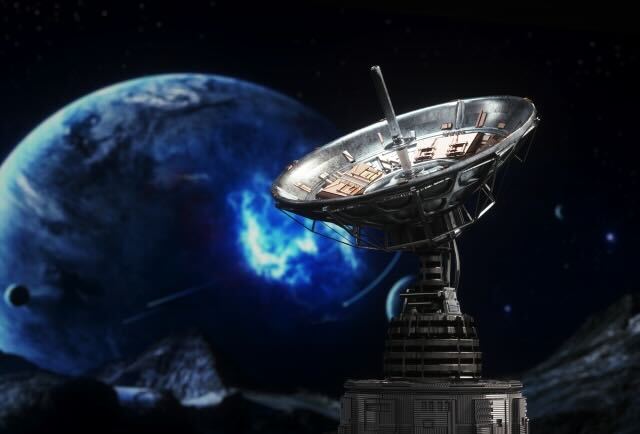
エンジン部品や着陸装置部品、衛星や無人航空機の軽量部品をつくるための製造法が半固体鋳造です。
その名のとおり、金属を完全に溶かさずに固体と液体が共存するシャーベット状態で成形する鋳造法です。液体から凝固しかけの状態にもっていく方法を『レオキャスティング』、固体を溶かしかけの状態にもっていく方法を『チクソキャスティング』と呼びます。使用される金属は、前文にもあるアルミニウム合金・マグネシウム合金・チタン合金などがあります。
金属を固体・液体の間の温度に加熱し、半固体状態の金属へせん断処理を施し流動性を高めます。半固体金属を高圧で金型に注入し、急速に凝固させます。
精密鋳造と同じく複雑な形状が作れることや、薄肉のものが作れ軽量化が可能。また、液体から個体間の体積変化を抑えられるためヒケ巣などの欠陥(※)に強くなり高品質の製品が作れることも特徴です。
反対に湯回り・充填不良が発生する可能性が高いため、温度・流動性・成分の管理は通常の通常法に比べ非常にシビアな管理方法が必要となってきます。
※鋳物製造で発生する鋳造欠陥とは?~種類・原因・対策を解説~
3Dプリンティング技術
鋳造で使用する原型や鋳型を3Dプリンティング技術で製造し、従来の鋳造技術と組み合わせて生産することで、複雑形状部品の製造が可能となりました。3Dプリンティングをすることで設計の自由度を高めることができ、従来の鋳造方法では製造が困難・不可能だった部品の生産が可能となりました。
3Dプリンターで原型を作れることはもちろん、鋳型自体を作る砂型積層プリンターもあります。金型製作が不要なため、少量生産や一点物の製造もできコスト効率の向上につながる事や、設計から試作段階もデータを修正して再試作ができるなど、開発期間やコストを大幅に短縮することが可能となりました。
その他にも、大型部品を作れる砂型鋳造や、製品を均一で高強度にできる遠心鋳造法、寸法精度の高い部品を短時間で量産できるダイカストなど、鋳造技術は宇宙産業においても不可欠な製造技術の一つです。
特に、精密鋳造や半固体鋳造などの高度な技術が、ロケットや衛星の開発に貢献しています。今後も鋳造技術の進化が、宇宙開発の更なる発展を支えるでしょう✨
次回の記事もお楽しみに!