鋳物製造で、避けて通れない課題の一つが『鋳造欠陥』、いわゆる不具合品の発生です。
60年以上鋳物製品を作り続けている大洋産業でも、不具合品の発生は他人事ではありません。
鋳造欠陥はほとんどの場合が鋳造プロセス中に発生します。その範囲は、外観に現れるものから内部構造に影響を及ぼすものまで多岐にわたります。
今回の記事では、鋳造欠陥の代表的な種類、その原因と対策について解説させていただきます!
湯回り
注湯時に発生する不具合で、溶かした金属を鋳型へ流し込んだ際、隅々まで行き渡らないまま固まってしまい、製品の形が不十分となってしまいます。また、湯が溶けあわず写真のように切れ目が生じる場合もあります。
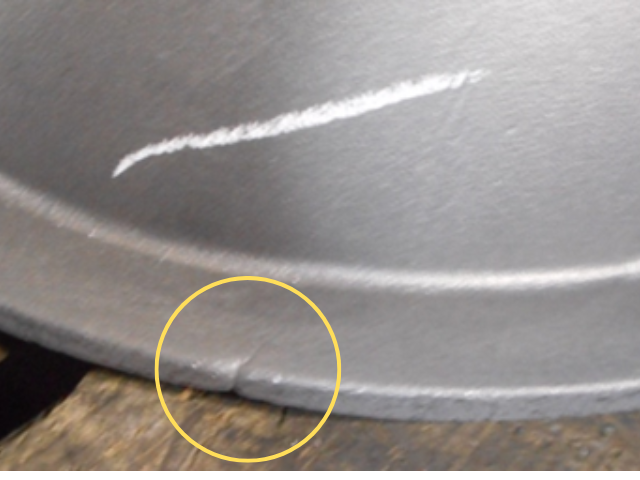
【原因】
湯の温度が低い、流し込みのスピードが遅い、鋳物の肉厚が薄い、湯道やセキの形状・位置が不適切など、湯回りでは様々な原因が考えられます。
【対策】
温度の管理、鋳込み速度を最適化する事により湯回りの不具合は改善されます。
湯口から遠い箇所で発生することが多いため、温度・速度で改善されない場合は湯道やセキ(※)の形状・位置を見直します。
※湯道・・・溶湯の注ぎ口から製品までの道となる部分
※セキ・・・湯道から直接製品に繋がる部分。湯口から湯道、セキまでを含めて「湯口系」や「鋳造方案」と呼ぶこともある。
砂くい/荒らされ
鋳型を砂で作る砂型鋳造(※)では、砂による不具合も発生します。
湯の流れに巻き込まれた砂が製品内部に入り込んでしまう「砂くい」や、湯の勢いに負けて鋳型内部の砂が剥がれてしまい、鋳肌が荒れる「荒らされ」などがあります。
※鋳型・製法による分類~砂型鋳造法について~
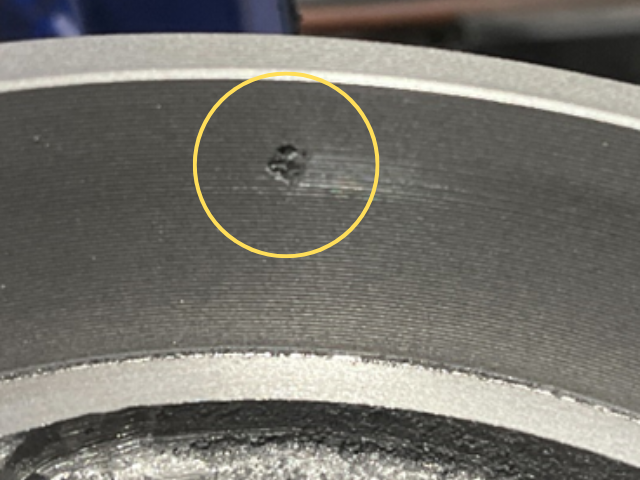
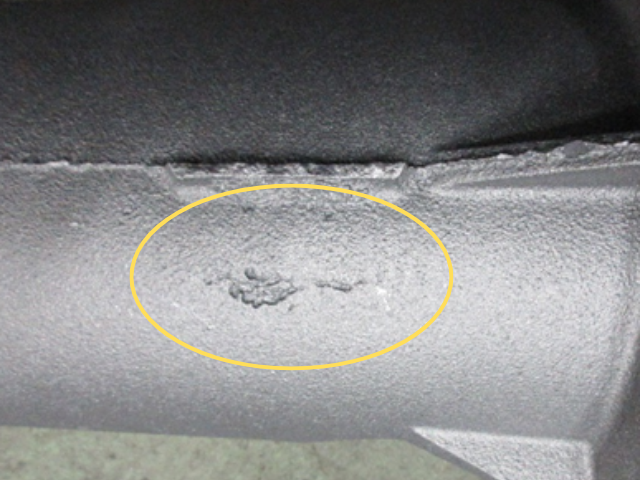
【原因】
一番の原因としては、砂に添加する粘結材・水分量が不十分であったり、撹拌が不十分で均一でないため、鋳物砂の強度が弱い、砂のつき固めが弱いなどがあげられます。
同じ製品で局所的に不具合が起こる際は、鋳造方案が良くなかったということも原因の一つとなります。
【対策】
砂の水分値や強度特性の改善、設備にも問題がないかを見直します。
湯が流れ込むセキを分散させ、湯の勢いがなるべく均等になるよう方案を見直したり、金型自体に破損や摩耗がないかチェックし、修正・更新・設計変更をかけることも対策の一つとなります。
割れ/欠け/打痕
凝固した後に発生する不具合として、冷却中やショットブラスト中に製品同士がぶつかり、割れたり欠けたりキズが付いてしまう事もあります。
見た目で分かる場合もありますが、微細な亀裂など見落としてしまう可能性もあるため、打音検査を行い音で判別する場合もあります。
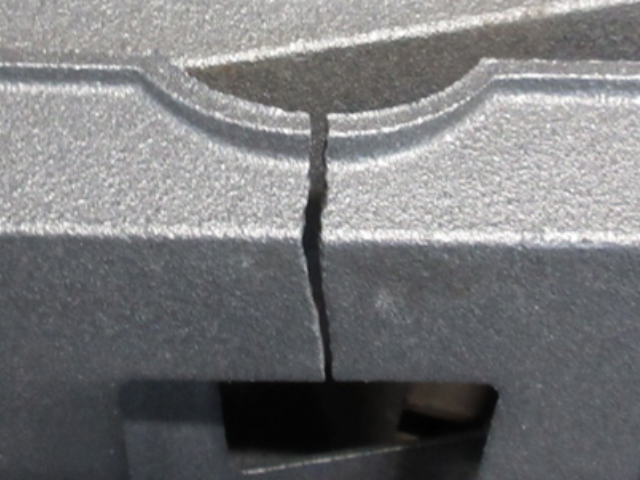
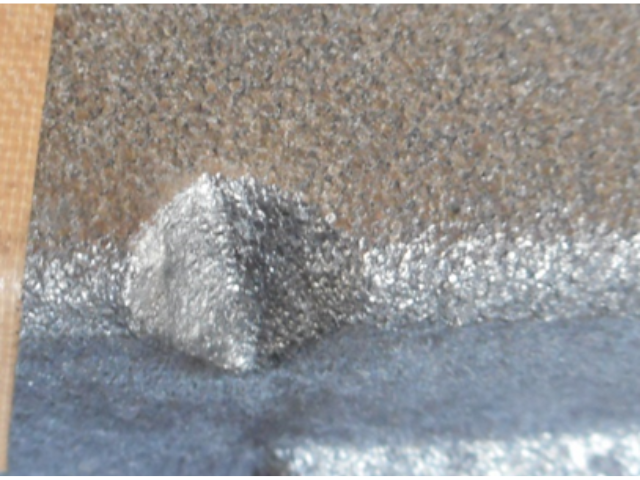
【原因】
割れ、欠け、打痕は製品同士の衝突で起こることがほとんどです。
【対策】
製品同士の衝突を避けるため、設備メンテナンスを行い製品の引っ掛かりを防いだり、ショットブラストをかける機械へ製品を入れるタイミングの調整をおこないます。大洋産業では、製品の種類が多いため、変形しやすい平べったい形状の製品はテーブルショット、内部の砂落ちが悪い袋形状の製品はエプロンショットという風に、製品に合わせたショットブラスト機械の使い分けも行っています。
ヒケ巣
見た目はしっかりと形が出来ているように見えますが、製品の内部に空洞ができる状態の不具合です。内部で起こる不具合は外観検査を素通りしてしまい、機械加工をかけた際に発見されることもあり、とても厄介な不具合です。
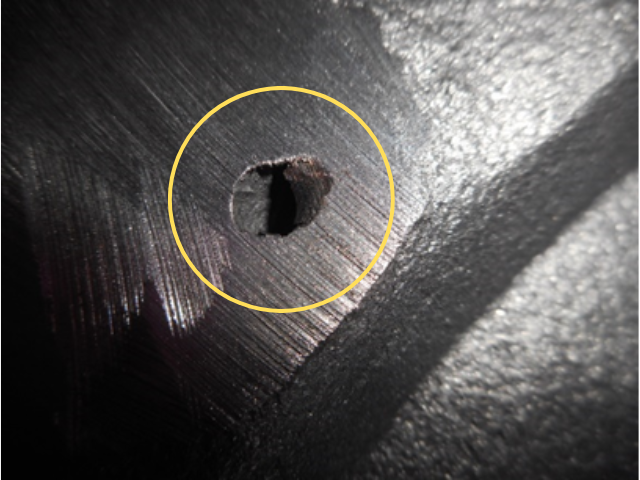
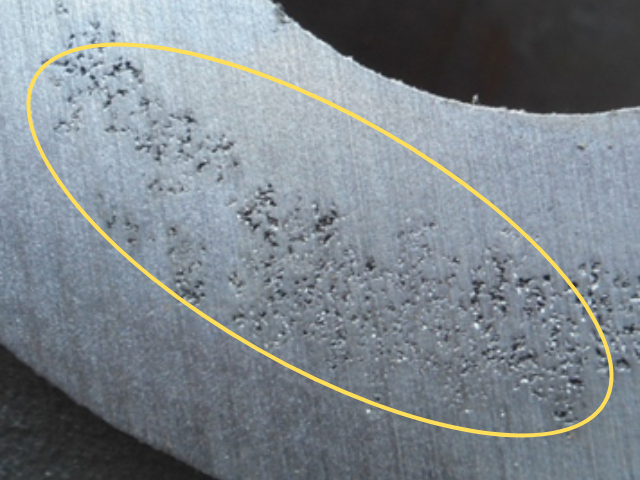
【原因】
ヒケ巣は、湯が固まる際に体積が減少し収縮することが原因です。特に、製品の肉厚部分は冷却に時間がかかるため、内部だけ液体のままの状態で周りが凝固収縮してしまうと、内部の体積が足りなくなり空洞が発生しやすくなります。
【対策】
対策は方案条件を絞り込み、ヒケを起こさないようにすることが重要です。
製品内部にハードスポット(※)が残らないよう、押し湯(※)を作り、押し湯部分が最後に固まるようにするなど、方案を見直します。
※ハードスポット・・・局所的に温度が高くなっているところ
※押し湯・・・収縮して減少した金属の不足分を補うための湯だまり部分
今回の記事では、鋳造欠陥について解説をさせていただきました!
不具合品の発生は品質問題はもちろんのこと、製造コストの増加・生産性の低下など様々な影響が出てしまいます。
大洋産業では今後もお客様に選ばれる企業を目指し、不具合品発生の防止・対策を日々行い、改善改良を続けていきます!
次回の記事もお楽しみに✨