前回、解説しました金型鋳造法に引き続き、鋳造法についての解説をしていきます。
今回はその他の特殊な鋳造法についてです。
前回までは、鋳型に砂や金型を用いた鋳造法を解説していましたが、今回の特殊鋳造法では原型となる模型に特殊な材質を用いたものや、製造機械自体が特殊なものをご紹介していきます。
精密鋳造法(せいみつちゅうぞうほう)

精密鋳造法とは、『ロストワックス』『インベストメント法』とも言われ、原型となる模型にロウ(ワックス)を使用した鋳造法です。
ロウで原型を作り、原型の周りを耐火性のある砂やセラミック、石膏などで固めて鋳型を作り、鋳型を加熱する事で中の原型(ロウ)を溶かして空洞を作り、溶かした金属を流し込む方法です。
ロウを溶かして空洞を作るため、模型を取り出す必要がなく、自由度が高く複雑な形状が作れることや、寸法精度が非常に高く表面も綺麗な仕上がりとなります。そのため、医療用器具、指輪等のアクセサリー類、航空機部品などが作られる事が多いです。
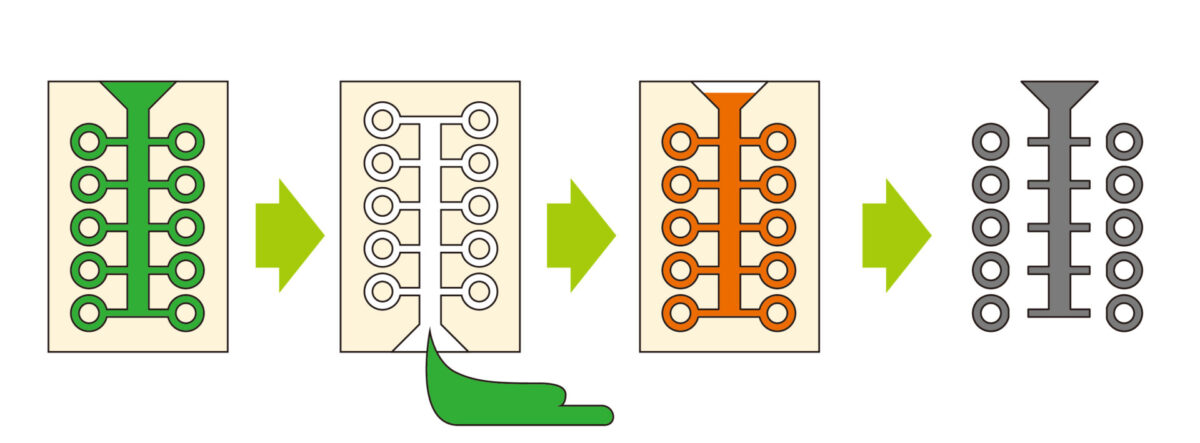
小さい製品であれば、上記図のように溶かした金属が製品流れるための湯道(ゆみち)に原型を複数繋ぎ合わせ、ツリーのような状態で量産する方法が一般的です。
鋳型が耐火物なので、高温のまま金属を流し込む事ができるため、金属の種類や製品の肉厚による制限が少ない点や、初期費用を抑えられる点はメリットと言えます。また、鋳型を分割して模型を取り出す必要がないため、設計段階で製品分割面や部品数を減らし、結果的にコスト削減に繋げられることもあります。
一方で、原型を毎回作る必要があり、耐火物の乾燥や脱ロウ(ロウを溶かす)工程等、コストや時間がかかるので大量生産に向いていない点はデメリットとなります。
遠心鋳造法(えんしんちゅうぞうほう)
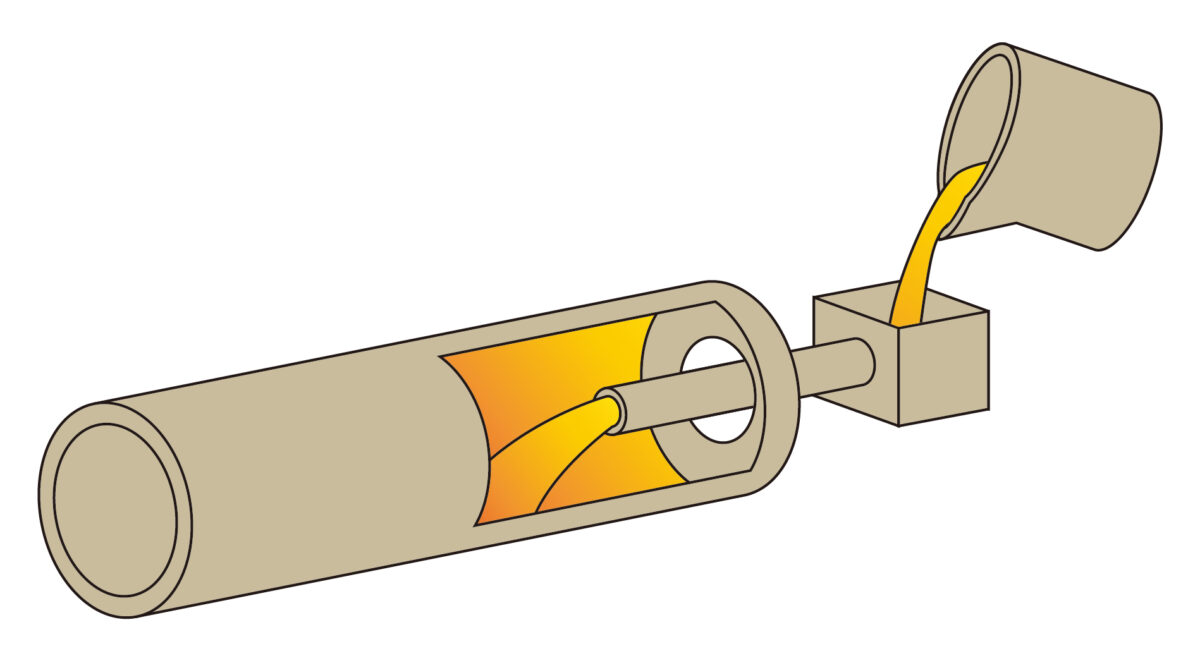
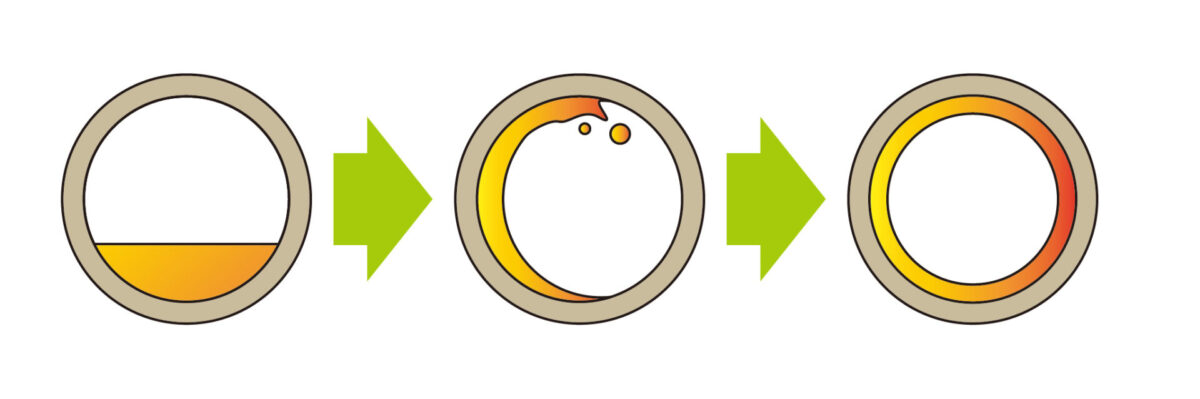
遠心鋳造法は、円筒形状の型を使用する『横型遠心鋳造法』・回転軸中心に湯口、外側に型を配置した『縦型遠心鋳造法』があります。今回は横型の鋳造法を解説します。
円筒形状の型へ溶かした金属を流し込み、型を高速回転させ遠心力によってパイプ状の鋳物が形成される方法で、上下水道用のパイプ管が代表的な製品です。
製品の空洞部分となる中子(なかご)を用いず生産できる事や、この方法では製品を繋ぐ湯口系を必要としない点や、遠心力の働きにくい不純物が分離され緻密な鋳物が形成される点がメリットと言えます。
製品形状によっては遠心力による材質の偏りや、厚さのある製品を作る事が難しい点などのデメリットもあります。
連続鋳造法(れんぞくちゅうぞうほう)
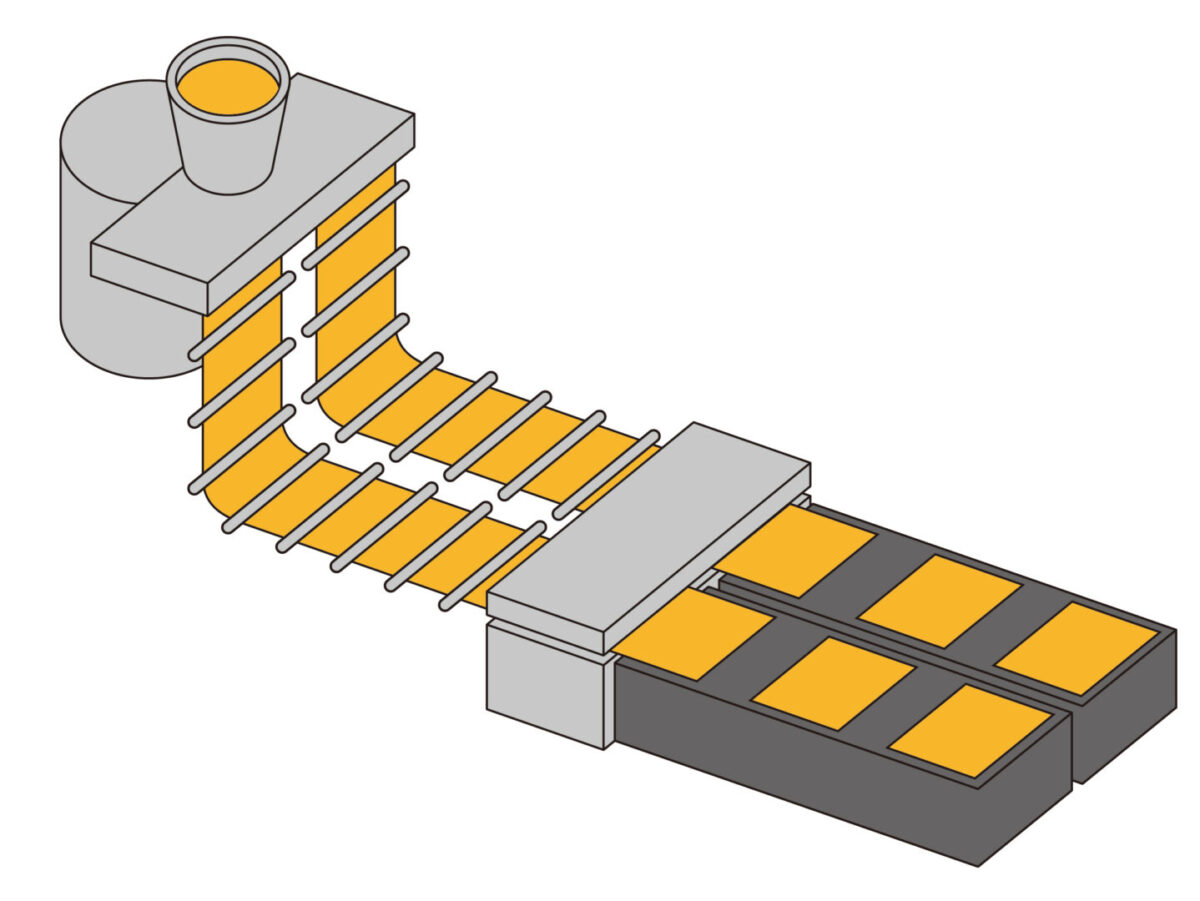
連続鋳造法では、溶かした金属を連続的に鋳型に注ぎ続け、鋳型内で冷却し途中で製品を切断していく方法で、代表的なものでは鉄鋼の生産等で利用される事があります。
大規模な『連続鋳造機』と呼ばれる機械によって製造され、金型の形状により丸棒・パイプ・角材・異形材と様々な棒状製品を作る事も可能です。
通常の鋳造法では注ぎ始めや注ぎ終わりの部分に内部欠陥や不純物が多く出やすいため、設計上であえて駄肉をつけて切り落とす場合もありますが、連続鋳造では絶えず一定の製品形状で出てくるため、切り捨てる部分が非常に少なく大量生産に向いている点はメリットとなります。
一方で、不純物・介在物や傘下に対して厳しく管理する必要があり、鋳型を水冷しながら長時間鋳込んでいる関係上、圧力や温度の変化によって割れたり変形を引き起こす恐れがある点は注意が必要となる事、機械設備の初期費用が高額になる点はデメリットとなります。
今回は特殊鋳造法の一例を解説させていただきました!
今まで砂型・金型・その他特殊型と様々な鋳物の製造法について解説させていただきました。
今後も鋳物についての解説を引き続きご紹介させていただきます。
次回の解説もお楽しみに✨